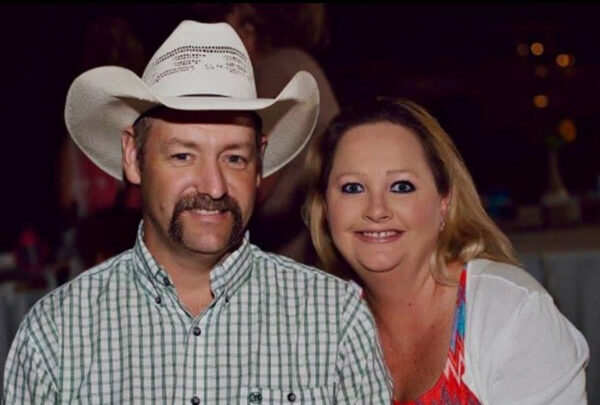
We provide fully integrated facility solutions that ensure the execution of capital projects across markets, offering local presence and global reach to the private and public sectors.
With broad-based expertise across disciplines, we are an unparalleled source for performance-driven facilities built to deliver, from concept to ribbon-cutting.
With a broad range of in-house engineering expertise, we can optimize your current operations or take your new project from concept to completion, providing unrivaled service and results.
Haskell is a global network of experts providing integrated design, engineering, construction and professional services to clients and communities.
Home / News & Insights / 6 Reasons Cans Are Better for Wine Packaging
From brunches to baseball games, the popularity growth in wine consumption, particularly among younger generations, is leading wine makers to consider a packaging option previously relegated almost exclusively to the beer and soda industry: cans.
As the Millennial generation ages into their late 20s and 30s, it is overtaking Baby Boomers when it comes to drinking wine. According to a 2017 survey by the Wine Market Council, Millennials now account for about 33 percent of wine drinkers, ranking just behind the Baby Boomers who make up 36 percent. With the gap between these two groups slowly closing, the wine industry is evaluating ways to adapt to changing trends, even if it means letting go of some long-held notions.
Thanks to this youthful surge in wine drinkers, the public perception of cans is shifting. Instead of associating cans with a perceived lower value, consumers are enjoying the convenience of cans that allow them to easily take their favorite rosé to the ballpark or the beach.
Manufacturers are also shifting their perceptions on cans as they provide many added benefits over bottles, including:
From a production standpoint, aluminum cans are far cheaper to make than glass bottles. Cans are also less breakable than glass bottles, resulting in fewer instances of lost product and materials due to manufacturing and shipping accidents. The more durable nature of cans also means there’s less of a need for secondary packaging such as the corrugated partitions used to separate wine bottles.
Can production lines require fewer equipment units in operation and consequently take up less floor space in a facility than a typical bottling line. Additionally, because cans are more stable than wine bottles (especially those with a reverse taper or higher center of mass), the can lines can move at higher speeds, increasing daily production potential. Most importantly, the reduction of equipment units of operation translates to a higher OEE (Overall Equipment Effectiveness).
Outside of a wine cellar, glass bottles don’t provide much protection from sunlight and other elements that can turn a good wine bad. Aluminum cans, however, are not penetrated by UV Rays and remain more tightly sealed than a corked bottle. This ensures that the product will be consumed at its highest level of quality.
When it comes to the finished product, cans offer the ability to cube pallet load with higher density than bottles. They’re also lighter, which reduces the energy cost for transportation to warehouses and distribution centers.
From a marketing standpoint, wine bottles offer minimal real estate when it comes to label imagery. Conversely, cans can be completely wrapped for maximum branding impact. It’s also more cost effective to switch out a shrink sleeve for special one-off runs than it is to change out a cold glue labeler for a wine bottle.
Changing a bottling line from 750 ml to 1.5-liter bottles requires extensive modifications to the equipment, PLCs and automation controls that can cost manufacturers time and money. But can production lines that maintain the same diameter can easily undergo a height changeover.
As the popularity of cans grows, wine makers aren’t the only alcohol industry taking notice. Canned cocktails are on the rise, too. If you’d like more information on the cost savings and added efficiency of cans over bottles, contact Haskell’s team of Beer, Wine and Spirits packaging experts.
For more information, contact Haskell’s Beer, Wine & Spirits division leader, Anthony White.
Haskell delivers $2+ billion annually in Architecture, Engineering, Construction (AEC) and Consulting solutions to assure certainty of outcome for complex capital projects worldwide. Haskell is a global, fully integrated, single-source design-build and EPC firm with over 2,600 highly specialized, in-house design, construction and administrative professionals across industrial and commercial markets. With 25+ office locations around the globe, Haskell is a trusted partner for global and emerging clients.
Coffee drinkers in the United States and Europe combine to brew in the neighborhood of 150 million Keurig coffee pods daily....
Designing a food production facility requires owners and operators to thoroughly consider many factors — capital...
Steam-in-Place (SIP) Operations, often used in the food and life sciences industries, use the thermal energy of condensing...
Packaging requires a wide array of machinery and systems, usually made by different original equipment manufacturers...
Simulation provides companies with unparalleled insight into operations and a unique competitive advantage in the marketplace....
At Haskell, we’re frequently asked about accumulation on packaging lines. How much is right for a line? Which type of accumulator...
Speed to the market is considered one of the advantages of integrated project delivery, but what Haskell’s project team...
Engineers at a large consumer products company believe they have an intractable code problem with a laner. Unbalanced...
Consumers’ habits have changed drastically in recent years, steered by the pandemic, nutritional trends, environmental...
Since she became the director of Haskell’s packaging operations and its Atlanta office in late 2016, Bela Jacobson’s career...
A flat start-up curve can ruin your game. Demand goes unmet. Startup costs rise. And despite your best efforts to reach capacity,...
No one knew quite what to expect at Pack Expo — the mega trade show billed as the world’s most comprehensive packing...
This year’s Pack Expo, scheduled for September 27-29 amid the bright lights of Las Vegas, Nevada, will highlight the manufacturing...
In addition to its accustomed practice of developing Project Engineers organically, Haskell currently has immediate...
Haskell’s Atlanta-based Controls and System Analytics teams recently stress-tested a major international distiller...
Production line anomalies that adversely affect plant operations are frustrating. It’s worse when the problem can’t...
Integrating a controls systems in a process and/or packaging line is a complex undertaking. Many companies claim the ability...
I have always been fascinated by the design aspect of product packaging, but I have not really considered the mechanics...
Automation and controls bring packaging lines to life with as much — or little — human assistance as desired for consumer...
From filling to capping to labeling to case packing — and every step in between — Haskell’s packaging systems designers...
For Emily Moseley, engineering isn’t only a job. Inspired by a former teacher and mentor, Moseley discovered her interest...
As a construction manager in Haskell’s Mexico City office, Waldo Salado delivers solutions. Salado helps to lead projects...
Have you been challenged to install a packaging line quickly? This is becoming a frequent occurrence as companies strive...
If you’ve read our blog series “How to Build a Distillery,” you probably have a good, high-level overview of the steps it...
A client came to us with a familiar problem: Their bottling line was fraught with multiple efficiency and quality problems....
Inventory management is the process of managing the flow of goods through a system. Although deciding where and when to...
A clean-in-place (CIP) system is among the largest users of consumables at a hygienic processing plant. Presented here...
Every large capital project will have unplanned and unexpected costs because it’s simply impossible to foresee and plan...
This paper will succinctly define OEE, provide examples of its contributing components, and share best practices for...
Experience shows that project success directly correlates to the team chosen to accomplish the project goals. Research...
Designing a packaging line can be a complex task. In order to describe the process to our clients, our team has found it helpful...
A great football team required great talent, but talent alone does not guarantee success. Players need to be trained to...
The ability to guide clients with data-driven decisions that maximize their return on investment is critical in any manufacturing...
With any processing plant, uncertainty presents unique challenges when managing capacity for growth. Will adding or...
Are you looking for ways to maximize the return on investment in your facility? Most manufacturers are. With this client...
How do you translate process design knowledge to other disciplines in a timely fashion? Our process-engineering team...
Seemingly, we’re all on the go. People constantly find ways to do more with the same amount of time. Some people join a teleconference...
What if shifts in consumer demand drive your organization to manufacture a new trending product? What if you need to build...
Whether you are a food, beverage, fine chemical or pharmaceutical manufacturer, there are questions that are common to...
Are you tired of traffic? Do you want the answers to solve all of your traffic woes? Unless everyone in your city reads this...
Are your process systems sterile? Steam-in-Place (SIP) Operations are used in the food and biotechnology industries,...
The beam simply does its job. Principals dictated by the laws of physics authenticate the beam as a yeoman of industrial...
Stop reading this blog — not forever, just for a few seconds. Look away from your screen and take in everything around you....
Simulation software that uses a physics engine can exponentially increase the advantages of manufacturing system design,...
While product-line simulation helps to address potential issues during the design phase, product-line emulation extends...
The race to market in consumer packaged goods is teeming with obstacles along the design, testing, manufacturing and distribution...
701 San Marco Boulevard
Jacksonville, FL 32207
© 2025 Haskell. All rights reserved.
We collect basic analytics to improve your experience. No personal data is stored. By continuing to use this site, you acknowledge this. For more details, see our Privacy Policy.