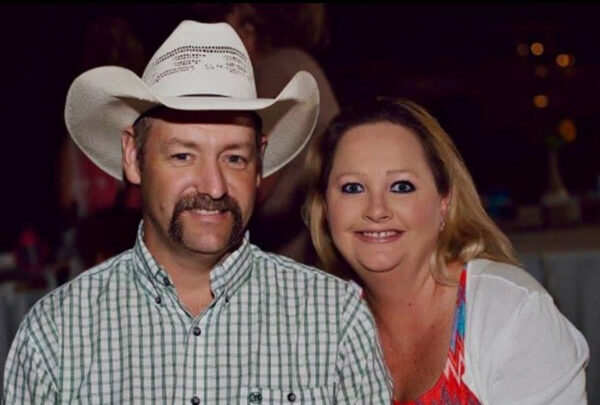
We provide fully integrated facility solutions that ensure the execution of capital projects across markets, offering local presence and global reach to the private and public sectors.
With broad-based expertise across disciplines, we are an unparalleled source for performance-driven facilities built to deliver, from concept to ribbon-cutting.
With a broad range of in-house engineering expertise, we can optimize your current operations or take your new project from concept to completion, providing unrivaled service and results.
Haskell is a global network of experts providing integrated design, engineering, construction and professional services to clients and communities.
Home / News & Insights / Elevate SIP Practices: 10 Expert Tips for Effective Sterile Operations
Steam-in-Place (SIP) Operations, often used in the food and life sciences industries, use the thermal energy of condensing steam for a controlled time period to affect a bioburden reduction
SIP Operations may be used for varying purposes, including the following:
The most stringent SIP application achieves sterile conditions throughout the entire equipment set with the goal of sterilizing the process system as an entity. The process system may include processing vessels and piping, filtered gas overlay supplies, process liquid filters, valves, pumps and processing instrumentation.
Haskell’s process engineering team has prepared a list of 10 effective rules to help you reliably achieve sterile conditions when SIP’ing a process equipment set. Enjoy!
Perform effective CIP operations prior to initiating SIP operations to remove processing soils. The thermal resistance of microorganisms and spores can be enhanced by the protective effects of process soil.
Operations should confirm steam supply header pressure and temperature to ensure a saturated steam supply. Superheated steam or an insufficient steam supply will result in a failed SIP program. Steam quality in the food industry must meet “Culinary Steam” requirements and in the biotech industry, specifications for “Clean Steam” must be met.
The SIP operations should be configured to introduce the saturated steam supply as high as possible in the equipment set, leveraging the steam supply pressure and temperature differences to push out ambient system gases through monitored process low points. The ambient gases will sink to process low points for effective evacuation.
Install steam trap blocking valves and a steam trap at each process low point and include a temperature monitoring device between the valve and steam trap to monitor temperature at each process low point. Be sure to locate the element above the trap’s condensate leg for accurate temperature measurement. If possible, use trap bypass valves for efficient air purging at the process low point to minimize the mixing of steam and air.
The importance of complete air elimination from the processing system cannot be overstated. To assist in the complete replacement of air with saturated steam, use monitored high-point air bleeds to push high air pockets out of the system. High-point air bleeds are recommended on large filter housing, process vessel vent and overlay gas supply lines.
Whenever possible, avoid parallel steam paths within the processing system sharing a common steam trap. As pressure differences occur during air removal stages, parallel lines pocket air, which prevents proper steam exposure, and results in sterility failures.
Plan the SIP operation to have steam flow in the same direction as the process flow to take advantage of the existing process piping pitch and support for process drainability. Plan the piping system to avoid hoses, dead-ends, and non-drainable low points that can create condensate pools or air pockets. These pools and air pockets can provide an insulating effect on the targeted microorganisms. Prompt and effective condensate elimination is critical to the SIP Operation’s success.
After process air has been fully removed and the system charged with saturated steam, a time delay is recommended for all system components to achieve the desired set point temperature. To achieve sterile conditions, universally expose the system to the FDA Center for Biologics Evaluation and Research (CBER) 21 CFR Guideline (Section 600.11) Time – Temperature Relationship of 121.5°C for 20 minutes. Consider adding an additional 1.5°C to the SIP set point to cover temperature element accuracy concerns. The 20-minute thermal exposure must be continuous, without the temperature dropping below the set point.
Providing a means of active steam flow to the process as the SIP timer counts down can help ensure the required thermal treatment has been achieved. This steam “activity” can be achieved by positioning the process vessel vent pressure control valve slightly open, or through the use of orificed steam traps or bypass valves.
After the desired exposure to saturated steam has been achieved for a complete thermal bio-kill, the sterile process boundary must be protected as the condensate is drained from the system. The equipment is cooled to prepare for sterile process operations.
Once the sterile boundary has been created, the question is often raised “How does one protect and maintain a sterile process boundary?” The use of overlapping sterile boundaries, active or passive air overlays, and steam blocks can be employed with great success.
About the author: Mike Byron is Haskell’s lead process engineer and has been with the company since 1993. He is intensively involved in Process/CIP/SIP system design for food and pharmaceutical manufacturing facilities. His diverse process engineering knowledge includes automated sterile/aseptic processing systems for cell culture, harvest, purification and sterile filling operations. He earned bachelor’s degrees in agricultural engineering and biochemistry from Purdue University.
Contact our Process Engineering team to learn more about maintaining sterile conditions or to discuss your specific facility.
Haskell delivers $2+ billion annually in Architecture, Engineering, Construction (AEC) and Consulting solutions to assure certainty of outcome for complex capital projects worldwide. Haskell is a global, fully integrated, single-source design-build and EPC firm with over 2,600 highly specialized, in-house design, construction and administrative professionals across industrial and commercial markets. With 25+ office locations around the globe, Haskell is a trusted partner for global and emerging clients.
Coffee drinkers in the United States and Europe combine to brew in the neighborhood of 150 million Keurig coffee pods daily....
Designing a food production facility requires owners and operators to thoroughly consider many factors — capital...
Packaging requires a wide array of machinery and systems, usually made by different original equipment manufacturers...
Here’s a question most consumers don’t ponder when biting into their favorite greasy cheeseburger: How much water did...
Clean-in-place (CIP) and steam-in-place (SIP) are essential pieces of the cleaning puzzle for manufacturing facilities,...
Simulation provides companies with unparalleled insight into operations and a unique competitive advantage in the marketplace....
At Haskell, we’re frequently asked about accumulation on packaging lines. How much is right for a line? Which type of accumulator...
Speed to the market is considered one of the advantages of integrated project delivery, but what Haskell’s project team...
Engineers at a large consumer products company believe they have an intractable code problem with a laner. Unbalanced...
Consumers’ habits have changed drastically in recent years, steered by the pandemic, nutritional trends, environmental...
Since she became the director of Haskell’s packaging operations and its Atlanta office in late 2016, Bela Jacobson’s career...
A flat start-up curve can ruin your game. Demand goes unmet. Startup costs rise. And despite your best efforts to reach capacity,...
No one knew quite what to expect at Pack Expo — the mega trade show billed as the world’s most comprehensive packing...
This year’s Pack Expo, scheduled for September 27-29 amid the bright lights of Las Vegas, Nevada, will highlight the manufacturing...
In addition to its accustomed practice of developing Project Engineers organically, Haskell currently has immediate...
Construction safety training, such as fall protection and proper protocols for excavation and ladder safety, is a common...
Production line anomalies that adversely affect plant operations are frustrating. It’s worse when the problem can’t...
Integrating a controls systems in a process and/or packaging line is a complex undertaking. Many companies claim the ability...
I have always been fascinated by the design aspect of product packaging, but I have not really considered the mechanics...
Automation and controls bring packaging lines to life with as much — or little — human assistance as desired for consumer...
For more than 50 years, Haskell has served as a leader in the architecture, engineering and construction industry, driven...
From filling to capping to labeling to case packing — and every step in between — Haskell’s packaging systems designers...
The food and beverage industry is a demanding world. Businesses must quickly respond to a market that’s constantly changing...
For Emily Moseley, engineering isn’t only a job. Inspired by a former teacher and mentor, Moseley discovered her interest...
As a construction manager in Haskell’s Mexico City office, Waldo Salado delivers solutions. Salado helps to lead projects...
Have you been challenged to install a packaging line quickly? This is becoming a frequent occurrence as companies strive...
If you’ve read our blog series “How to Build a Distillery,” you probably have a good, high-level overview of the steps it...
A client came to us with a familiar problem: Their bottling line was fraught with multiple efficiency and quality problems....
Inventory management is the process of managing the flow of goods through a system. Although deciding where and when to...
From brunches to baseball games, the popularity growth in wine consumption, particularly among younger generations,...
A clean-in-place (CIP) system is among the largest users of consumables at a hygienic processing plant. Presented here...
Every large capital project will have unplanned and unexpected costs because it’s simply impossible to foresee and plan...
This paper will succinctly define OEE, provide examples of its contributing components, and share best practices for...
Experience shows that project success directly correlates to the team chosen to accomplish the project goals. Research...
Designing a packaging line can be a complex task. In order to describe the process to our clients, our team has found it helpful...
A great football team required great talent, but talent alone does not guarantee success. Players need to be trained to...
The ability to guide clients with data-driven decisions that maximize their return on investment is critical in any manufacturing...
With any processing plant, uncertainty presents unique challenges when managing capacity for growth. Will adding or...
Are you looking for ways to maximize the return on investment in your facility? Most manufacturers are. With this client...
How do you translate process design knowledge to other disciplines in a timely fashion? Our process-engineering team...
Seemingly, we’re all on the go. People constantly find ways to do more with the same amount of time. Some people join a teleconference...
What if shifts in consumer demand drive your organization to manufacture a new trending product? What if you need to build...
Whether you are a food, beverage, fine chemical or pharmaceutical manufacturer, there are questions that are common to...
Are you tired of traffic? Do you want the answers to solve all of your traffic woes? Unless everyone in your city reads this...
Are your process systems sterile? Steam-in-Place (SIP) Operations are used in the food and biotechnology industries,...
The beam simply does its job. Principals dictated by the laws of physics authenticate the beam as a yeoman of industrial...
Stop reading this blog — not forever, just for a few seconds. Look away from your screen and take in everything around you....
Simulation software that uses a physics engine can exponentially increase the advantages of manufacturing system design,...
While product-line simulation helps to address potential issues during the design phase, product-line emulation extends...
The race to market in consumer packaged goods is teeming with obstacles along the design, testing, manufacturing and distribution...
701 San Marco Boulevard
Jacksonville, FL 32207
© 2025 Haskell. All rights reserved.
We collect basic analytics to improve your experience. No personal data is stored. By continuing to use this site, you acknowledge this. For more details, see our Privacy Policy.