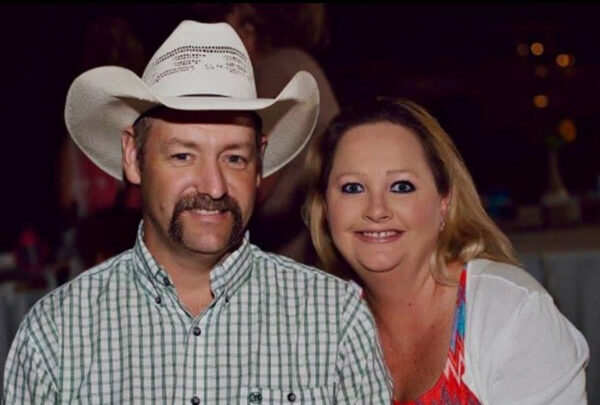
We provide fully integrated facility solutions that ensure the execution of capital projects across markets, offering local presence and global reach to the private and public sectors.
With broad-based expertise across disciplines, we are an unparalleled source for performance-driven facilities built to deliver, from concept to ribbon-cutting.
With a broad range of in-house engineering expertise, we can optimize your current operations or take your new project from concept to completion, providing unrivaled service and results.
Haskell is a global network of experts providing integrated design, engineering, construction and professional services to clients and communities.
Home / News & Insights / Case Study: Controlling an Out-of-Control System
A client came to us with a familiar problem: Their bottling line was fraught with multiple efficiency and quality problems.
The line, which included a new packer and sealer with associated empty-carton, full-carton and full-bottle conveyor systems, produced numerous issues that the original integrator was unable to resolve:
Haskell’s packaging automation team investigated each of the issues and, within two days, turned over a system that was balanced and jam-free. The following is a summary of the steps taken for each problem area.
The Haskell team employed our core conveyor control strategy and recalculated the conveyor speeds based on the bottle sizes and conveyor width to derive desired speeds in bottles per minute. Once this was complete, the packer and bottle conveyor speeds were modified to follow each other based on the status of the packer infeed sensors (Low, Medium and High). With a proper bottle-per-minute relationship established between the packer and the bottle conveyor, bottle pressure was eliminated and the packer was able to maintain steady-state operation rather than varying speeds and occasionally stopping because of to low bottle prime.
Due to long, non-accumulating sections of conveyor prior to the packer, the empty-case system was not supplying a steady flow of empty cases to the packer, resulting in frequent low-prime situations. In an attempt to resolve the issue, the original turnkey supplier added an accumulation mode to help close gaps, but this action instead increased case pressure at the curves and created case jams. As a result, the accumulation mode was disabled, leaving the system unable to adequately supply empty cases to the packer.
To solve the issue, Haskell’s team once again relied on the basics. We recalculated the conveyor speeds based on the length of the case and the desired speed of the packer. Once the conveyor speeds were established, the conveyor logic was modified to follow the speed of the packer rather than relying on the preset speeds previously used.
To manage the issue of gaps, the conveyor logic was modified to accumulate further upstream and properly meter cases through the curve instead of trying to accumulate through the curve. When larger-than-expected gaps were detected on non-accumulating conveyors, the conveyor speeds would modulate to close the gap. By the time the cases were on the last non-accumulating conveyor, a large decline belt, there was a consistent flow of cases heading to the packer, which eliminated the frequent low prime issue.
When downstream issues caused the case sealer to stop, cases would jam at the sealer discharge. After investigating, the team determined that there was not enough physical space to properly run out the sealer. Stopping the sealer in place was not an option, because doing so would result in cases not sealing properly and frequent stops due to open flaps.
To resolve the issue, the team recalculated the conveyor speeds based on the length of the case and the desired bottles-per-minute speed of the sealer. Once this relationship was in place, the team calculated and implemented the space and conveyor speeds necessary to create the physical space required to run out the sealer.
By employing the basics of relating product sizes to conveyor speeds, Haskell can improve a system that isn’t operating as expected. This method can also be used to optimize systems that are layout constrained. Following these methods takes the guesswork out of line control and results in a system that runs reliably with minimal product loss or damage.
Haskell delivers $2+ billion annually in Architecture, Engineering, Construction (AEC) and Consulting solutions to assure certainty of outcome for complex capital projects worldwide. Haskell is a global, fully integrated, single-source design-build and EPC firm with over 2,600 highly specialized, in-house design, construction and administrative professionals across industrial and commercial markets. With 25+ office locations around the globe, Haskell is a trusted partner for global and emerging clients.
Coffee drinkers in the United States and Europe combine to brew in the neighborhood of 150 million Keurig coffee pods daily....
Designing a food production facility requires owners and operators to thoroughly consider many factors — capital...
Steam-in-Place (SIP) Operations, often used in the food and life sciences industries, use the thermal energy of condensing...
Packaging requires a wide array of machinery and systems, usually made by different original equipment manufacturers...
Simulation provides companies with unparalleled insight into operations and a unique competitive advantage in the marketplace....
At Haskell, we’re frequently asked about accumulation on packaging lines. How much is right for a line? Which type of accumulator...
Speed to the market is considered one of the advantages of integrated project delivery, but what Haskell’s project team...
Engineers at a large consumer products company believe they have an intractable code problem with a laner. Unbalanced...
Consumers’ habits have changed drastically in recent years, steered by the pandemic, nutritional trends, environmental...
Since she became the director of Haskell’s packaging operations and its Atlanta office in late 2016, Bela Jacobson’s career...
A flat start-up curve can ruin your game. Demand goes unmet. Startup costs rise. And despite your best efforts to reach capacity,...
No one knew quite what to expect at Pack Expo — the mega trade show billed as the world’s most comprehensive packing...
This year’s Pack Expo, scheduled for September 27-29 amid the bright lights of Las Vegas, Nevada, will highlight the manufacturing...
In addition to its accustomed practice of developing Project Engineers organically, Haskell currently has immediate...
Production line anomalies that adversely affect plant operations are frustrating. It’s worse when the problem can’t...
Integrating a controls systems in a process and/or packaging line is a complex undertaking. Many companies claim the ability...
I have always been fascinated by the design aspect of product packaging, but I have not really considered the mechanics...
Automation and controls bring packaging lines to life with as much — or little — human assistance as desired for consumer...
From filling to capping to labeling to case packing — and every step in between — Haskell’s packaging systems designers...
For Emily Moseley, engineering isn’t only a job. Inspired by a former teacher and mentor, Moseley discovered her interest...
As a construction manager in Haskell’s Mexico City office, Waldo Salado delivers solutions. Salado helps to lead projects...
Have you been challenged to install a packaging line quickly? This is becoming a frequent occurrence as companies strive...
If you’ve read our blog series “How to Build a Distillery,” you probably have a good, high-level overview of the steps it...
Inventory management is the process of managing the flow of goods through a system. Although deciding where and when to...
From brunches to baseball games, the popularity growth in wine consumption, particularly among younger generations,...
A clean-in-place (CIP) system is among the largest users of consumables at a hygienic processing plant. Presented here...
Every large capital project will have unplanned and unexpected costs because it’s simply impossible to foresee and plan...
This paper will succinctly define OEE, provide examples of its contributing components, and share best practices for...
Experience shows that project success directly correlates to the team chosen to accomplish the project goals. Research...
Designing a packaging line can be a complex task. In order to describe the process to our clients, our team has found it helpful...
A great football team required great talent, but talent alone does not guarantee success. Players need to be trained to...
The ability to guide clients with data-driven decisions that maximize their return on investment is critical in any manufacturing...
With any processing plant, uncertainty presents unique challenges when managing capacity for growth. Will adding or...
Are you looking for ways to maximize the return on investment in your facility? Most manufacturers are. With this client...
How do you translate process design knowledge to other disciplines in a timely fashion? Our process-engineering team...
Seemingly, we’re all on the go. People constantly find ways to do more with the same amount of time. Some people join a teleconference...
What if shifts in consumer demand drive your organization to manufacture a new trending product? What if you need to build...
Whether you are a food, beverage, fine chemical or pharmaceutical manufacturer, there are questions that are common to...
Are you tired of traffic? Do you want the answers to solve all of your traffic woes? Unless everyone in your city reads this...
Are your process systems sterile? Steam-in-Place (SIP) Operations are used in the food and biotechnology industries,...
The beam simply does its job. Principals dictated by the laws of physics authenticate the beam as a yeoman of industrial...
Stop reading this blog — not forever, just for a few seconds. Look away from your screen and take in everything around you....
Simulation software that uses a physics engine can exponentially increase the advantages of manufacturing system design,...
While product-line simulation helps to address potential issues during the design phase, product-line emulation extends...
The race to market in consumer packaged goods is teeming with obstacles along the design, testing, manufacturing and distribution...
701 San Marco Boulevard
Jacksonville, FL 32207
© 2025 Haskell. All rights reserved.
We collect basic analytics to improve your experience. No personal data is stored. By continuing to use this site, you acknowledge this. For more details, see our Privacy Policy.