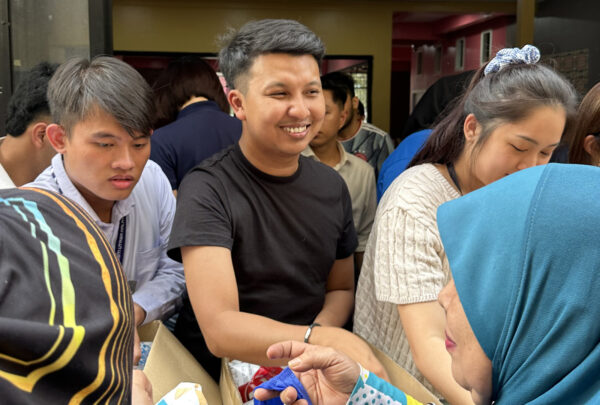
We provide fully integrated facility solutions that ensure the execution of capital projects across markets, offering local presence and global reach to the private and public sectors.
With broad-based expertise across disciplines, we are an unparalleled source for performance-driven facilities built to deliver, from concept to ribbon-cutting.
With a broad range of in-house engineering expertise, we can optimize your current operations or take your new project from concept to completion, providing unrivaled service and results.
Haskell is a global network of experts providing integrated design, engineering, construction and professional services to clients and communities.
Home / News & Insights / Haskell Keeps Expanding and Improving Use of DMC Delivery
Design Manufacture Construct (DMC) project delivery is growing in popularity, and as an early adopter, Haskell continues to improve its methods and expand its use of the highly efficient construction method.
On a DMC project, modular building components are fabricated off-site in a manufacturing facility, then shipped to the project site for assembly by a smaller crew than would be needed for traditional on-site construction. Advantages include shortened schedules, cost savings, improved safety, higher quality and greater environmental sustainability.
“DMC is a delivery model that provides customers with consistent quality and a shorter delivery time,” said Ryan Hollister, Vice President of Haskell’s Manufacturing Core. “DMC allows for the manufacturing process to begin early, in parallel with site development. Unlike traditional construction, DMC projects can begin manufacturing and construction before the site is ready for development. The advantage of DMC’s quicker delivery times cannot be overstated, especially for time-sensitive customers who need to begin operations as soon as possible.”
Working with its strategic partner BLOX, a firm specializing in manufacturing components for the healthcare industry, Haskell is the prime contractor on numerous free-standing emergency room projects for Universal Health Services and has completed past DMC projects for HCA Healthcare and Walmart Health.
BLOX builds the modular components, called ubers, at its 1 million-square-foot manufacturing facility in Bessemer, Alabama, and ships them to the project location, where Haskell crews assemble, construct and deliver the facility. Haskell handles all preconstruction and construction management and often self-performs large portions of the work.
Haskell has also partnered with other manufacturing firms based on the unique needs of DMC projects. As an example, Haskell uses different manufacturers, including BLOX, to build different elements of projects for a global program building religious structures for a confidential client.
“DMC requires a different buying methodology,” Hollister said. “DMC customers usually seek standardization and serial programming. This means that DMC is a perfect solution for customers desiring standardization of facilities, since repeatability and scalability are DMC’s forte.”
Interestingly, DMC has offered an added, and unexpected, advantage recently. Much of the construction industry has been choked by widespread shortages of building materials, as producers have been slow to ramp back up since the COVID-19 lockdown ended, and labor shortages. Steel shortages are particularly severe in the cases of joists and joist girders.
DMC answers each of those challenges.
First, modular building is less labor-intensive, requiring smaller crews to assemble prefabricated components, so a workforce shortage is less onerous. And secondly, the consistent nature of the manufacturing process helps insulate it against supply chain anomalies and interruptions.
“A DMC facility has more consistent inventory than a traditional construction site,” Hollister said. “It’s easier to forecast material needs because a manufacturing facility knows what materials it needs to mass produce certain goods. This doesn’t mean shortages or delays won’t be problematic. For examples, car manufacturers have been ravaged by the chip shortage. But since DMC facilities have to mass produce buildings and structures, they have a greater existing supply of prefabricated materials than a traditional construction site would.”
Haskell delivers $2+ billion annually in Architecture, Engineering, Construction (AEC) and Consulting solutions to assure certainty of outcome for complex capital projects worldwide. Haskell is a global, fully integrated, single-source design-build and EPC firm with over 2,600 highly specialized, in-house design, construction and administrative professionals across industrial and commercial markets. With 25+ office locations around the globe, Haskell is a trusted partner for global and emerging clients.
Edwin Cortez was a self-professed “swamp rat” from the bayous of Louisiana without much of an education to speak of. But...
For the fourth year in a row and the 19th overall, Haskell Steel has received the American Institute of Steel Construction...
With an assist from Haskell Steel, a team of senior civil engineering students from the University of North Florida (UNF)...
Steel, the backbone of numerous significant construction projects, not only creates the framework for large industrial...
Haskell Steel, the company’s owned and operated steel fabrication facility in Jacksonville, Florida, historically...
Dysruptek, Haskell’s venture capital and innovation arm, works to find technologies that can improve the day-to-day...
From its origin with five employees in the corner of a warehouse, Haskell Steel has grown to a 50-plus-person operation...
People use that Contact Us link up at the top of the Haskell.com website for all sorts of reasons, but as far as anyone knows,...
Free-Standing Emergency Departments (FSEDs) are, by definition, a community’s link to healthcare when residents need...
Guy Stenzel, Estimating Manager in Haskell’s Manufacturing Core, tracks current events like a TV news producer, charts...
One day at the Haskell Steel fabrication facility, two team members were rotating a piece of steel weighing hundreds of...
Welders, steel-fitters and even job-seekers looking to learn those valuable trades should mark their calendars for a...
With business growing and its demand for steel at an all-time high, Haskell is seeking to add welders to its steel fabrication...
Recently, a Haskell Healthcare Construction project experienced an immediate need for steel fabrication to meet a scheduled...
The world of venture capital and startups might seem more about revolution than evolution. Still, the recent bankruptcy...
Over the past year, the Architectural, Engineering and Construction (AEC) industry has been rocked by price surges in...
In the same way that Design-Build project delivery revolutionized the construction industry by enhancing design and...
William “Butch” Rowe well remembers the early days in the Haskell steel shop. Today, Haskell Steel is rightfully regarded...
In 1976, Haskell established its Permanent Craft Employee (PCE) program, extending full-time employment and company...
In the same way that it pioneered the Design-Build method of project delivery decades ago, Haskell is distinguishing itself...
JACKSONVILLE, FL – Haskell, one of the leading global architecture, engineering, construction (AEC) and consulting...
When Anheuser-Busch, the world’s largest beer producer, broke ground on a $175 million expansion to their Metal Container...
701 San Marco Boulevard
Jacksonville, FL 32207
© 2025 Haskell. All rights reserved.
We collect basic analytics to improve your experience. No personal data is stored. By continuing to use this site, you acknowledge this. For more details, see our Privacy Policy.