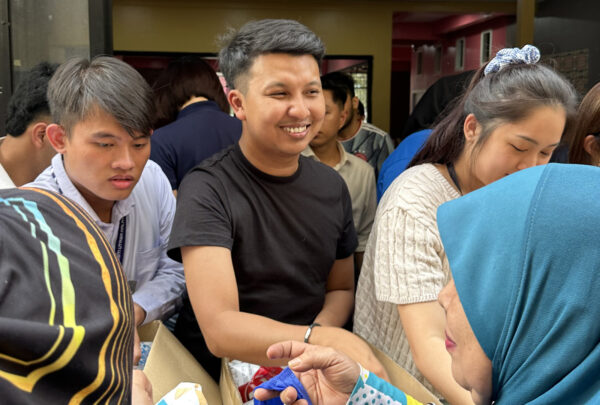
We provide fully integrated facility solutions that ensure the execution of capital projects across markets, offering local presence and global reach to the private and public sectors.
With broad-based expertise across disciplines, we are an unparalleled source for performance-driven facilities built to deliver, from concept to ribbon-cutting.
With a broad range of in-house engineering expertise, we can optimize your current operations or take your new project from concept to completion, providing unrivaled service and results.
Haskell is a global network of experts providing integrated design, engineering, construction and professional services to clients and communities.
Home / News & Insights / Haskell Steel Ensures Certainty with Expertise and Cutting-Edge Tech
From its origin with five employees in the corner of a warehouse, Haskell Steel has grown to a 50-plus-person operation using state-of-the-art technology on a 30-acre campus and 100,000 square feet of facility space.
Haskell Steel Director Touan Plante, who joined Haskell in 2010 and leads onsite operations, said that the origins of Haskell Steel are integral to Haskell’s journey as a leader in the design-build industry.
From its earliest days, Haskell has been a user and innovator in tilt-up construction, an efficient method in which concrete slabs are cast horizontally at the jobsite. Once cured, the slabs are picked by crane and set in place, creating a wall from a series of consecutive panels standing next to each other.
Forming the concrete panels required steel.
Early on, Haskell depended on fabricators throughout the country for its steel needs, which meant it was subject to price fluctuations and delivery delays that resulted in critical schedule impacts. In the mid-1970s, the decision was made to take control of its own supply chain, and Haskell Steel was created.
Operating from rented warehouse space with limited space and equipment, Haskell Steel began making embedded plates and angles for tilt-up panels. By 1980, a push for increased self-reliance drove them to create a production facility capable of providing all the steel necessary for Haskell projects.
“As the company continued to grow and take on larger and more complex projects, Haskell Steel grew and evolved with the company,” Vice President of Manufacturing Ryan Hollister said. “Haskell Steel has been purpose-built for the complexities and speed required for integrated AEC projects, and our facility is designed to be flexible and adapt to the diverse range of projects Haskell builds. Whether it is heavy structural fencing to contain elephants, an aircraft mega-hangar or a manufacturing facility, our team is prepared to handle it.”
The presence of in-house steel resources offers advantages beyond certainty of supply. Traditionally, consideration of steel fabrication occurs near the end stages of project procurement. But at Haskell, the steel team has a seat at the table early in the conceptual design process, which allows its experts in procurement, fabrication, and installation to provide design input, weigh production options, and begin procurement and fabrication much earlier than the conventional approach allows. This shortens the project lifecycle by months.
Haskell’s aggressive application of technology in every stage of steel production also sets it apart.
Innovative technology and equipment provide Haskell Steel the ability to punch well above its weight class. Robotic manufacturing and 3D design tools improve safety and quality by automating steps of the fabrication process; this has the benefit of both reducing the team’s exposure to hazards and providing precision beyond the capabilities of manual operations.
While the improvements to efficiency are important, the ability to provide Haskell Steel craftsmen with a safe working environment elevates morale and is core to Haskell’s philosophy of providing team members with the best job of their life. Haskell Steel’s safety record reflects this. In an industry where everything is hot, heavy, and sharp, Haskell Steel boasts an impressive record of zero incidents in more than three years.
Nowhere has the breadth and range of Haskell Steel been better displayed than on the recently completed Norwegian Cruise Line Terminal B at PortMiami. Haskell Steel joined conversations early in the creation of the terminal’s iconic curvilinear design and took the lead on the steel design detailing, material procurement, fabrication, logistics, and erection of more than 8,200 tons of steel. Haskell Steel fabricated steel at its own facility, managed a network of thirteen sub-fabricators, centralized procurement, managed the logistics of shipping by road, rail and water, and led erection in the field.
Haskell also is a trusted source of steel and start-to-finish project management for other contractors and owners. It recently delivered for one client five structures totaling 3.3 million square feet of roof area, and while it averages annual production of about 6,000 tons, its integrated design experience and toolset enable it to oversee much larger projects than firms without the breadth of services Haskell provides. Haskell Steel managers benefit from the same training and resources all Haskell managers receive. This provides the team with the tools, training, and support available to a company the size and scale of Haskell without losing the flexibility and nimbleness that smaller companies can provide.
And its capabilities have been certified by the American Institute of Steel Construction continuously since achieving the designation in 2009.
“It’s a rigorously audited quality program,” Plante said. “AISC sets the standard for quality in our industry. The AISC certification means a fabricator strictly adheres to the best industry practices. Every year, AISC auditors conduct on-site inspections of our complete operation, measuring quality, safety, training and management practices. AISC certification requires us to continuously improve and keep our saw sharp.”
In Spring 2022, Haskell acquired Ocoee, Florida-based Cortez Incorporated, a mechanical and process contractor with more than 50 employees and nearly 100 years of experience in fabrication, installation and maintenance, serving primarily the food and beverage industry.
Cortez expands Haskell’s integrated capabilities to serve its customers with an acuity that has made it the No. 1-ranked Food & Beverage Manufacturing Contractor by Engineering News-Record two of the past three years and one of the top Consumer Packaged Goods service providers in the U.S.
“The acquisition of Cortez expands our toolbox into stainless steel fabrication,” Hollister said. “They’re oftentimes contracted by owners directly or by equipment manufacturers, so that will give us a lot of valuable insight into our clients’ needs.”
Haskell Steel’s expertise, technology and collaborative approach can cut months off of your project timeline. Contact the Haskell Steel team to discuss the options.
Haskell delivers $2+ billion annually in Architecture, Engineering, Construction (AEC) and Consulting solutions to assure certainty of outcome for complex capital projects worldwide. Haskell is a global, fully integrated, single-source design-build and EPC firm with over 2,600 highly specialized, in-house design, construction and administrative professionals across industrial and commercial markets. With 25+ office locations around the globe, Haskell is a trusted partner for global and emerging clients.
Haskell has long been at the forefront of implementing Building Information Modeling (BIM) technology, streamlining...
Edwin Cortez was a self-professed “swamp rat” from the bayous of Louisiana without much of an education to speak of. But...
For the fourth year in a row and the 19th overall, Haskell Steel has received the American Institute of Steel Construction...
With an assist from Haskell Steel, a team of senior civil engineering students from the University of North Florida (UNF)...
Steel, the backbone of numerous significant construction projects, not only creates the framework for large industrial...
It’s a ritual for architecture, engineering and construction (AEC) industry publications to weigh in with predictions...
Haskell Steel, the company’s owned and operated steel fabrication facility in Jacksonville, Florida, historically...
Dysruptek, Haskell’s venture capital and innovation arm, works to find technologies that can improve the day-to-day...
In the evolving world of civil engineering, innovation is the driving force behind progress. Haskell Civil Engineers...
Mentioning beer, wine and spirits may bring to mind festive settings and good times with friends, but make no mistake: The...
As a pioneer in design-build delivery, Haskell always has worked across the architectural, engineering and construction...
Guy Stenzel, Estimating Manager in Haskell’s Manufacturing Core, tracks current events like a TV news producer, charts...
One day at the Haskell Steel fabrication facility, two team members were rotating a piece of steel weighing hundreds of...
Welders, steel-fitters and even job-seekers looking to learn those valuable trades should mark their calendars for a...
In what is, to date, a rare engagement at the University of Florida in Gainesville, design-build delivery will soon produce...
With business growing and its demand for steel at an all-time high, Haskell is seeking to add welders to its steel fabrication...
Recently, a Haskell Healthcare Construction project experienced an immediate need for steel fabrication to meet a scheduled...
Before the Jacksonville Jaguars could imagine the future, they needed to envision the present, and they asked Haskell,...
Design Manufacture Construct (DMC) project delivery is growing in popularity, and as an early adopter, Haskell continues...
Over the past year, the Architectural, Engineering and Construction (AEC) industry has been rocked by price surges in...
When presented with the opportunity to share best practices with construction industry professionals in Latin America,...
William “Butch” Rowe well remembers the early days in the Haskell steel shop. Today, Haskell Steel is rightfully regarded...
Haskell’s structural engineering team helps clients solve unique challenges – such as designing an explosion room or...
Intelligent growth is a delicate balance between adopting the latest manufacturing advancements to improve overall...
Construction is one of history’s oldest trades, and it remains one of the most old-fashioned. Working to make the most of...
David Bates grew up working is the family construction business, majored in construction management at Auburn and then...
In 1976, Haskell established its Permanent Craft Employee (PCE) program, extending full-time employment and company...
As the coronavirus pandemic disrupted business worldwide, project delays and shutdowns swept across the construction...
These days, Sonny Carter is an experienced and accomplished project superintendent with Haskell, responsible for planning...
Haskell and geotechnical partner Building and Earth Sciences will receive a National Recognition Award from the American...
Growing up near St. Louis, Todd Miller originally wanted to design roller coasters, so much so that it led him to a physics...
When Anheuser-Busch, the world’s largest beer producer, broke ground on a $175 million expansion to their Metal Container...
Bryan Bedell, Division Leader of Haskell’s Water Division, takes a moment to answer five questions about key issues...
Are you tired of traffic? Do you want the answers to solve all of your traffic woes? Unless everyone in your city reads this...
701 San Marco Boulevard
Jacksonville, FL 32207
© 2025 Haskell. All rights reserved.
We collect basic analytics to improve your experience. No personal data is stored. By continuing to use this site, you acknowledge this. For more details, see our Privacy Policy.