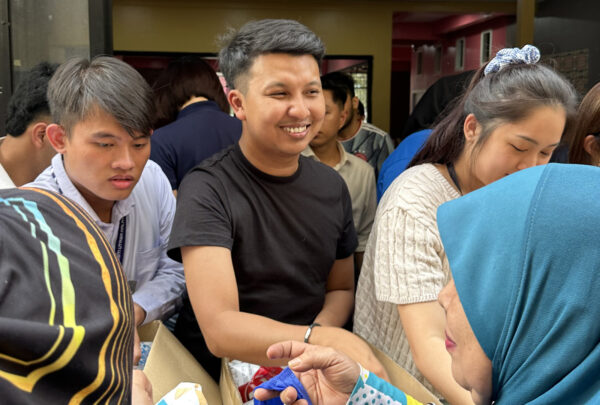
We provide fully integrated facility solutions that ensure the execution of capital projects across markets, offering local presence and global reach to the private and public sectors.
With broad-based expertise across disciplines, we are an unparalleled source for performance-driven facilities built to deliver, from concept to ribbon-cutting.
With a broad range of in-house engineering expertise, we can optimize your current operations or take your new project from concept to completion, providing unrivaled service and results.
Haskell is a global network of experts providing integrated design, engineering, construction and professional services to clients and communities.
Home / News & Insights / Design-Build’s Flexibility was on Full Display at Rocket Test Facility
Before rocket science becomes the exacting discipline that sends man and machine into space, it’s science fiction. And while Blue Origin’s plans for a tank cleaning and testing (TCAT) building on its Rocket Factory campus in Merritt Island, Florida, weren’t some fanciful galivant through the cosmos, they included a host of unknowns that had to be resolved as construction was underway.
Blue Origin is the American aerospace manufacturer and sub-orbital spaceflight services company founded in 2000 by Jeff Bezos to make access to space cheaper and more reliable through reusable launch vehicles.
In 2015, Blue Origin chose Haskell for a series of projects, including TCAT, which would be only the second facility of its kind in the world.
“They knew they needed a building, but they didn’t know exactly what they needed,” said David Schoening, Design Director of Public Facilities, who was the design manager on the project. “They were still very much working on their program and what their needs were. We started design while they were still working on writing the program and their criteria.”
One of the significant advantages of design-build project delivery is speed, and Blue Origin chose Haskell because of its reputation for just that. With an anticipated launch schedule, the rocket maker wanted the facility’s testing capabilities online as soon as possible as it developed the New Glenn heavy-lift orbital launch vehicle.
“They hired us to be fast, and we got started before they knew what they needed,” Schoening said. “They literally needed to be in the building as soon as possible. Rocket design, I’ve learned, is iterative. You don’t usually get it right the first time you test.”
The testing that would take place in the facility would replicate the extreme pressures a rocket would experience as it was launched and propelled through the atmosphere. The 224-foot-tall TCAT structure was built to withstand hurricane-force winds externally and multidirectional forces internally to accommodate rigorous testing.
TCAT strained the limits of existing soil conditions, so Haskell’s structural engineers, geotechnical consultants, SMEs and contractors concluded that a system of 322 rigid inclusions would need to be installed to a depth of 90 feet below the building foundation to prevent the tower from sinking or leaning.
The final construction consisted of 9-foot and 7-foot mat foundations, , 3,500 tons of structural steel, seven steel catwalk platforms, an exterior elevator, multiple utilities and an HVAC system. It featured three hangar doors, one of which was 112 feet tall and 45 feet wide, and two cranes, the taller of which reached a hook height of 205 feet with a capacity of 100 tons.
However, the final construction resembled the original vision only conceptually. To wit:
“It evolved as they went,” Schoening said.
Even the variables came with variables. Because it had no single point of contact, Blue Origin’s changes came from numerous stakeholders. Further, requests frequently changed in response to revised testing criteria, which evolved until the project reached completion.
So how did the project finish under budget and three months early?
“It’s in our DNA. We always try to over-deliver for our clients,” Senior Project Manager Ivan Robles said.
TCAT came several structures into the Blue Origin campus, so Haskell’s project team knew the level of flexibility and collaboration that would be necessary and was able to leverage existing relationships.
Schoening and his designers held a charrette with client representatives and extrapolated as much information as possible. They held frequent meetings to present their work and to receive updates as the rocket program proceeded.
“When we would get criteria, we would always talk about, ‘Well, what margin do we need? Do we want to make the space a little bit bigger to accommodate if things were to change?’” Schoening said. “We worked flexibly with them. We tried not to overspend but to hedge our bets and add a little if we thought it might be helpful in the future: door sizes, ceiling heights, crane capacities, etc.”
Extensive collaboration between designers, builders and project owners is a hallmark of Haskell projects, but it has never been more critical. The field team sometimes had to implement changes before design documents were issued. Constant communication enabled fast action as conditions evolved.
“From the construction aspect, we were able to stay ahead of the game,” Robles said. “We were able to establish a good relationship with the stakeholders. Basically, our approach was, ‘Tell me, what you are trying to accomplish, and then I can tell you, from a construction perspective, what I can do. Then we can see if it is realistic.’”
Indeed, Blue Origin partnered with Haskell to keep the project moving. Sometimes, that meant keeping Blue Origin moving.
“When you’re dealing with stakeholders that are rocket scientists, they like to test their procedures 20 or 30 times until they get it perfect,” Robles said. “In construction, we can’t afford that. So, we had conversations with the client to understand the end goal. Then, we could say how we could do it in the field in a practical and cost-efficient way. It seems simple, but we were able to create a trusted relationship with the main stakeholders, and they would listen to us.”
That trust led Blue Origin to engage Haskell to design-build another facility of the same type, nicknamed “2CAT”, at the same campus to perform additional testing operations and further expedite their launch program schedule.
Solving complex architectural, engineering and construction projects with expertise and imagination is what we do. Contact us to discuss your facilities needs.
Haskell delivers $2+ billion annually in Architecture, Engineering, Construction (AEC) and Consulting solutions to assure certainty of outcome for complex capital projects worldwide. Haskell is a global, fully integrated, single-source design-build and EPC firm with over 2,600 highly specialized, in-house design, construction and administrative professionals across industrial and commercial markets. With 25+ office locations around the globe, Haskell is a trusted partner for global and emerging clients.
All Points, a leading technical services provider to the aerospace industry, and its Space Prep division, which offers...
When most air travelers see the drink cart rolling down the aisle, they think about what to order. Zary Peretz thinks of logistics....
Since its first aircraft hangar project more than three decades ago, Haskell has evolved into one of the world’s leading...
Haskell is investing in Florida’s Space Coast with the opening of its new Brevard County Regional Office. The office is...
Two of Haskell’s most prominent traits – strong relationship-building and the ability to provide speed to market – put...
Haskell to lead design and build of Aerion Park in Melbourne, Florida Work underway to prepare 110+ acre site for major construction...
These days, Sonny Carter is an experienced and accomplished project superintendent with Haskell, responsible for planning...
Haskell recently completed a new nacelle assembly facility for UTC Aerospace Systems in Foley, Alabama. The primary mission...
JACKSONVILLE, FL – Haskell recently completed the twin bay Maintenance, Repair and Overhaul (MRO) painting facility...
Aviation industry forecasts predict that the global commercial aircraft fleet will almost double in number by the year...
701 San Marco Boulevard
Jacksonville, FL 32207
© 2025 Haskell. All rights reserved.
We collect basic analytics to improve your experience. No personal data is stored. By continuing to use this site, you acknowledge this. For more details, see our Privacy Policy.