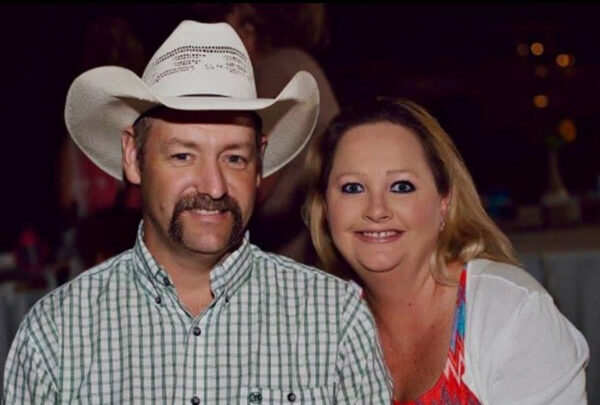
We provide fully integrated facility solutions that ensure the execution of capital projects across markets, offering local presence and global reach to the private and public sectors.
With broad-based expertise across disciplines, we are an unparalleled source for performance-driven facilities built to deliver, from concept to ribbon-cutting.
With a broad range of in-house engineering expertise, we can optimize your current operations or take your new project from concept to completion, providing unrivaled service and results.
Haskell is a global network of experts providing integrated design, engineering, construction and professional services to clients and communities.
Home / News & Insights / Material Handling Solutions Ensure Safe, Efficient Warehouse Logistics
Moving and accessing goods in a manufacturing facility requires ease of access, minimal touches and safety to operate smoothly. Haskell’s Material Handling and Distribution System design team conducts each segment to produce the greatest possible harmony.
Every manufacturer must store its raw materials and finished goods. The amount of storage space needed varies, but the need to store and move goods is a constant of every facility.
A large distribution center may require an automatic storage and retrieval system that delivers pallets with the push of a button. Others use standard racking, which stores pallets on metal shelves accessed by an operator using a forklift.
Haskell designs systems to move materials from truck to storage and from storage to and from the manufacturing line with efficiency and ease. Placing items near their point of use optimizes material flow and reduces travel time.
Haskell engineers, also called integrators, work with operators to understand how they interact with their systems, so equipment and pathway placement provide the best possible experience.
“They are the experts in their business,” said Bela Jacobson, Haskell Vice President of Packaging Operations. “They have insights for how it works beyond data.”
Haskell also optimizes material handling by reducing touches.
“The more you touch things, the less efficient it becomes,” Jacobson said. “Every touch is time. It is a risk of damaging the product, and it is a risk in safety.”
Automation reduces touches, as does optimal space utilization. The challenge is to balance storing as much as possible in a warehouse while also offering operators easy access.
In many warehouses, pedestrians and fork trucks share the same space. Haskell’s warehouse design minimizes the likelihood of interface between pedestrians and fork trucks, which improves the safety of warehouse personnel. Integrators validate their assumptions using simulation software.
“The fewer times they intersect, the fewer times they have for an accident,” Jacobson said.
Design simulation for proof of concept helps Haskell improve existing warehouses or design new ones. Often, clients come to Haskell when they add a new product stock-keeping units (SKUs) and need help finding space to store raw materials and finished goods.
“You either figure out how to make it work, or build a new space,” she said. “And our customers often want us to figure out how to make it work to optimize their capital budget.”
Haskell also performs capacity analysis and master planning to ensure that clients have available space for growth.
“We don’t want them to corner themselves into a solution that works today, but in one year it’s going to be outdated,” she said.
This holistic view is Haskell’s competitive differentiator.
As a design-build firm, Haskell doesn’t just design the warehouse layout. Its teams take facilities from the concept to commissioning, offering the cost savings and certainty of outcome that only come through integrated delivery.
“Understanding the whole process and not just a small part of the process helps drive a better design,” Jacobson said. “From the process side to the packaging side, we address all the different areas, so we understand how they work together. We design for the whole system, not just with blinders on for the warehouse.”
<!–
–>
Haskell delivers $2+ billion annually in Architecture, Engineering, Construction (AEC) and Consulting solutions to assure certainty of outcome for complex capital projects worldwide. Haskell is a global, fully integrated, single-source design-build and EPC firm with over 2,600 highly specialized, in-house design, construction and administrative professionals across industrial and commercial markets. With 25+ office locations around the globe, Haskell is a trusted partner for global and emerging clients.
Coffee drinkers in the United States and Europe combine to brew in the neighborhood of 150 million Keurig coffee pods daily....
Packaging requires a wide array of machinery and systems, usually made by different original equipment manufacturers...
From the project owner’s vantage point, integrated delivery offers a seamless, turnkey experience. From beginning to...
For the first few years, Alan Green’s presence at the American Craft Spirits Association (ACSA) annual convention was...
As Haskell’s Automation Practice Area Lead, Don Kocher is responsible for developing and maintaining corporate standards...
Production line anomalies that adversely affect plant operations are frustrating. It’s worse when the problem can’t...
Automation and controls bring packaging lines to life with as much — or little — human assistance as desired for consumer...
As a senior engineer for automation at Seiberling, a Haskell Company, Lon Reilly creates intricate electrical design...
A clean-in-place (CIP) system is among the largest users of consumables at a hygienic processing plant. Presented here...
How do you translate process design knowledge to other disciplines in a timely fashion? Our process-engineering team...
Are you tired of traffic? Do you want the answers to solve all of your traffic woes? Unless everyone in your city reads this...
701 San Marco Boulevard
Jacksonville, FL 32207
© 2025 Haskell. All rights reserved.
We collect basic analytics to improve your experience. No personal data is stored. By continuing to use this site, you acknowledge this. For more details, see our Privacy Policy.