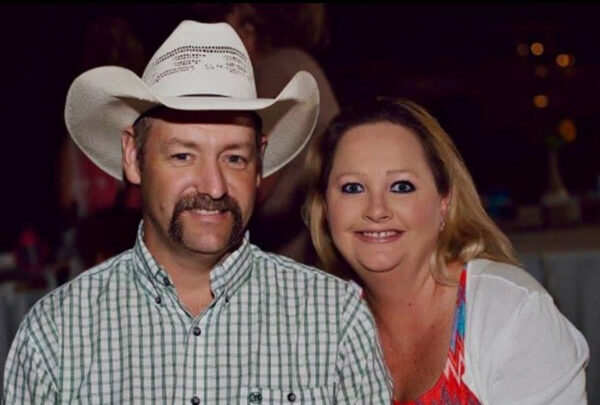
We provide fully integrated facility solutions that ensure the execution of capital projects across markets, offering local presence and global reach to the private and public sectors.
With broad-based expertise across disciplines, we are an unparalleled source for performance-driven facilities built to deliver, from concept to ribbon-cutting.
With a broad range of in-house engineering expertise, we can optimize your current operations or take your new project from concept to completion, providing unrivaled service and results.
Haskell is a global network of experts providing integrated design, engineering, construction and professional services to clients and communities.
Home / News & Insights / Case Study: Manufacturing Line Simulation Yields Six-Figure Savings
The scientific method is often mischaracterized as a static, linear process. However, real insight and discovery in science is an ongoing cycle of developing models and methods that provide greater accuracy and usefulness. Discovering better results requires an openness to different approaches in problem-solving.
The scientific method is often mischaracterized by the following straightforward sequence of steps:
Einstein demonstrated that science is not a recipe. All inquiry requires intelligence, imagination and creativity. Real insight and discovery require adaptability. For example, Einstein’s Theories of Relativity didn’t negate the foundational truth of Sir Isaac Newton’s Principia; they simply expanded and refined them.
At times, manufacturing engineering can fall into stale patterns and methodologies. The basic feasibility and design practices of many of these processes are sound, but they often fail to realize full potential for improvements.
This case study examines a case in which an engineering team went beyond basic feasibility and design practices, using incremental steps to realize a $500,000 savings.
The setting for this study is a massive manufacturing facility in the Southeastern U.S. Prior to this initiative, it comprised four miles of conveyor, 13 palletizing systems, 11 new tie-in points, 33 possible inputs and 13 destinations. Demand for the plant’s consumer products continues to grow, but equipment and operations need updating.
The company’s engineering team brought in Haskell professionals to conduct an initial engineering feasibility study that would help scope the project to determine initial funding needs.
This static capacity and linear analysis is, by definition, conservative, spreadsheet-type work. Once the feasibility study was completed, a more detailed, engineered project definition plan provided refined appropriation requirements, which initiated verification of a new layout for variables such as product demand curves, operating schedules, maintenance and selection of equipment.
Targets of opportunity were identified to justify or deny the capital investment for the system’s improvement. In this case, there were eight significant decision points established:
The definition report indicated that a new high-speed sorter likely needed to be added to meet production requirements. Then, the debate began.
The company’s engineering design team was satisfied with the static capacity reports and layout alternatives. The Haskell team had conducted a thorough analysis, and corporate leadership was ready to make an investment choice against the overall business case.
However, the Haskell team and some client members of the team had a nagging feeling. From their experience with other complex systems, the professionals knew there was more to be learned and revealed than the static reports could supply.
The local project team, comprising facility and Haskell engineers, drew on past successes as they encouraged corporate management to fund simulation of the design options, which would be similar to the cost of the static reports.
Haskell engineers knew that simulations would mimic specific characteristics of real systems dynamically and provide insight on system operations, performance, and verification of controls strategies for the entirety of Process, Packaging and Material Handling & Distribution systems. They contended that a full simulation of various design options would reveal superior design options for such a large and complex system.
Corporate management agreed, and their decision paid off. The simulation revealed that the new system was currently “overdesigned.” Careful study under multiple operating scenarios revealed several significant cost-saving changes:
Ultimately, by using simulation to mimic the entire system, the project team committed to slightly greater costs for the up-front engineering effort but realized a 10-fold return on that investment (ROI), saving approximately $500,000 on unneeded equipment and systems.
While there was nothing wrong with the data from the static analyses, real insight and discovery through the more sophisticated simulation models and methods ultimately provided greater accuracy and usefulness in the form of significant savings for the client.
Contact Haskell’s of Processing, Packaging and Material Handling experts to optimize your manufacturing systems and maximize ROI.
Haskell delivers $2+ billion annually in Architecture, Engineering, Construction (AEC) and Consulting solutions to assure certainty of outcome for complex capital projects worldwide. Haskell is a global, fully integrated, single-source design-build and EPC firm with over 2,600 highly specialized, in-house design, construction and administrative professionals across industrial and commercial markets. With 25+ office locations around the globe, Haskell is a trusted partner for global and emerging clients.
The ability to guide clients with data-driven decisions that maximize their return on investment is critical in any manufacturing...
Seemingly, we’re all on the go. People constantly find ways to do more with the same amount of time. Some people join a teleconference...
Simulation software that uses a physics engine can exponentially increase the advantages of manufacturing system design,...
701 San Marco Boulevard
Jacksonville, FL 32207
© 2025 Haskell. All rights reserved.
We collect basic analytics to improve your experience. No personal data is stored. By continuing to use this site, you acknowledge this. For more details, see our Privacy Policy.